Submersible Motors
Jayashree’s PMSM submersible motors are made with high-grade stainless steel; and are suitable for irrigation and drinking water solar pumping applications. These motors run at synchronous speed (zero slip) and are about 10%-15% more efficient than AC Induction Motors of the same rating. Thus delivering real, tangible benefits in solar pumping systems.
Solar pumps fitted with PMSM/BLDC submersible motors will start discharging water earlier in the day and will work for longer hours as compared to pumps fitted with AC motors – resulting in much more water delivery during the day.
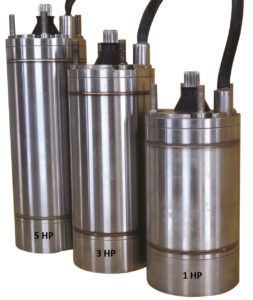
Product benefits:
- Large increase in efficiency and compact size compared to AC submersible motors
- Lowest energy costs due to high efficiency & power factor for partial load conditions.
- Excellent value for money solution for solar pumping applications due to higher water output for a given number of solar panels.
Submersible Motor Specifications:
- IS 9283 compliant
- IP68 grade protection
- Stainless steel casing, shaft & other components
- Equipped with mechanical seal and sand guard for maximum sand protection
- Insulation Class F
- Oil Filled or Water Filled designs
Oil / Water Filled (rated speed 3450 rpm) | |
0.5 HP | Panel Voltage: 35 – 90 VDC; Current Idc: 8.4 A Back emf: 10.2 Vrms/KRPM; Current Im = 7.6 Arms |
1 HP | Panel Voltage: 90 – 150 VDC; Current Idc: 8.4 A Back emf: 21 Vrms/KRPM; Current Im = 7 Arms |
2 HP | Panel Voltage: 180 – 270 VDC; Current Idc: 8.4 A Back emf: 32 Vrms/KRPM; Current Im = 8.5 Arms |
3 HP | Panel Voltage: 300 – 360 VDC; Current Idc: 8.4 A Back emf: 53 Vrms/KRPM; Current Im = 7.5 Arms |
5 HP | Panel Voltage: 400 – 600 VDC; Current Idc: 8.4 A Back emf: 90 Vrms/KRPM; Current Im = 7.6 Arms |
7.5 HP | Panel Voltage: 300 – 500 VDC; Current Idc: 16.8 A Back emf: 69 Vrms/KRPM; Current Im = 14 Arms |
Comparison of AC & BLDC Motors
# | SOLAR AC Induction Motor Driven Pumps | BLDC / Permanent Magnet Motor Driven Pumps |
1 | Induction motor (IM) efficiency is very poor for motors up to 5 HP (3.75 KW). IM efficiency is comparable to BLDC for motors of 5 KW and above. | Test results with 0.5 HP motors and 0.5 HP pump showed that the IM consumed 30% – 50% more power for same head & flow. The difference in consumption increased with Head. |
2 | ![]() Typical torque/speed curve for an Induction Motor Starting torque of IM is low compared to rated torque while starting current is 6-10 times rated current. | ![]() BLDC motors have a flat Torque/speed curve in the operating range. BLDC motors are capable of delivering the same torque from zero to rated speed. |
3 | Starting torque & current can be controlled by the inverter/VFD used to covert DC power from solar panels and drive the IM. However, this method results in torque pulses which can lead to cavitation and reduce the pump life. | BLDC motors can deliver high starting torque and the drive can work directly with the DC supply provided by the solar panels. This results in a smooth start at slow speed which is gradually increased to required operating speed. |
4 | It also becomes necessary to select an IM of higher rating (which means extra power consumption) than what would be indicated just by rated torque/speed. | BLDC motor can be selected to match the pump load and hence the power requirement is optimized resulting in optimal selection of solar panels. |
5 | AC Induction motor driven centrifugal pumps do not start in low solar insolation levels / low irradiance. (For developing the required pressure, the minimum speed / frequency required can be achieved at higher power inputs.) | BLDC motor driven pumps work in low solar insolation levels i.e. early start and late stop. Hence duration of working over a day is more resulting in increased water output. |
6 | For a typical duty of 90m, 5000 LPD by 1 hp capacity system, the Solar panel required (under practical field conditions) is 1800 Wp. Similarly for serving duty of 60m, 5000 LPD, it requires 1400 to 1500 Wp under practical conditions. Hence total costing of PV modules and mounting structure is significantly higher per system*. | For a typical duty of 90m, 5000 LPD by 1 hp capacity system, the Solar PV Module requirement (under practical field conditions) is 900 Wp only. Similarly for serving duty of 60m, 5000 LPD, it requires 600 to 750 Wp only under practical conditions. ** Savings in solar panel costs more than offset the higher cost of BLDC motor. |